Developing novel high-performance textile composites
- Project lead
- Simon McQueen-Mason
- Institute
- University of York
Summary:
The fashion industry, globally worth $700bn, utilised 110 millions tons of fibre in 2018 and has ranked the second most polluting industry in the world. Growing awareness of the impact of human consumption on the environment has led producers and consumers to look for more sustainable feedstocks and processes for textile production. (https://www.ellenmacarthurfoundation.org/publications/a-new-textiles-economy-redesigning-fashions-future). Bacterial cellulose has been suggested as a sustainable alternative for the biomanufacturing of textiles but the sheets of cellulose produced from the fermentation lack the durability and hydrophobicity that are needed in apparel applications.
Aims:
Aims were to generate composites with functional properties that will inspire the design of novel textiles, to develop a collaboration between designers to work with novel sustainable textiles and the academic groups focus on plant cell wall and material science, to lead to further funding.
Outcomes:
In this project, we have investigated the use of wheat straw to prepare bacterial cellulose and lignin and hemicellulose to modify its properties. The aim was to develop the production of Novel High-Performance composites with a specific interest in textile applications. Wheat straw hydrolysates were successfully used as feedstock for fermentation by acetobacter. Lignin nanoparticles were synthesised from the wheat straw pre-treatment liquor and increased the hydrophobicity of the composites, as could a wax sample extracted from the wheat straw. Further analysis showed the presence of non-cellulosic polysaccharides in the composites that were fermented in the presence of hemicellulose and this could have interesting consequences for its material properties. Manufacturing possibilities for new cellulosic textiles were investigated and weaving demonstrated for bacterial cellulose.
The project enabled the production of Proof of Principle that were used to apply for a Super Follow On with BBSRC.
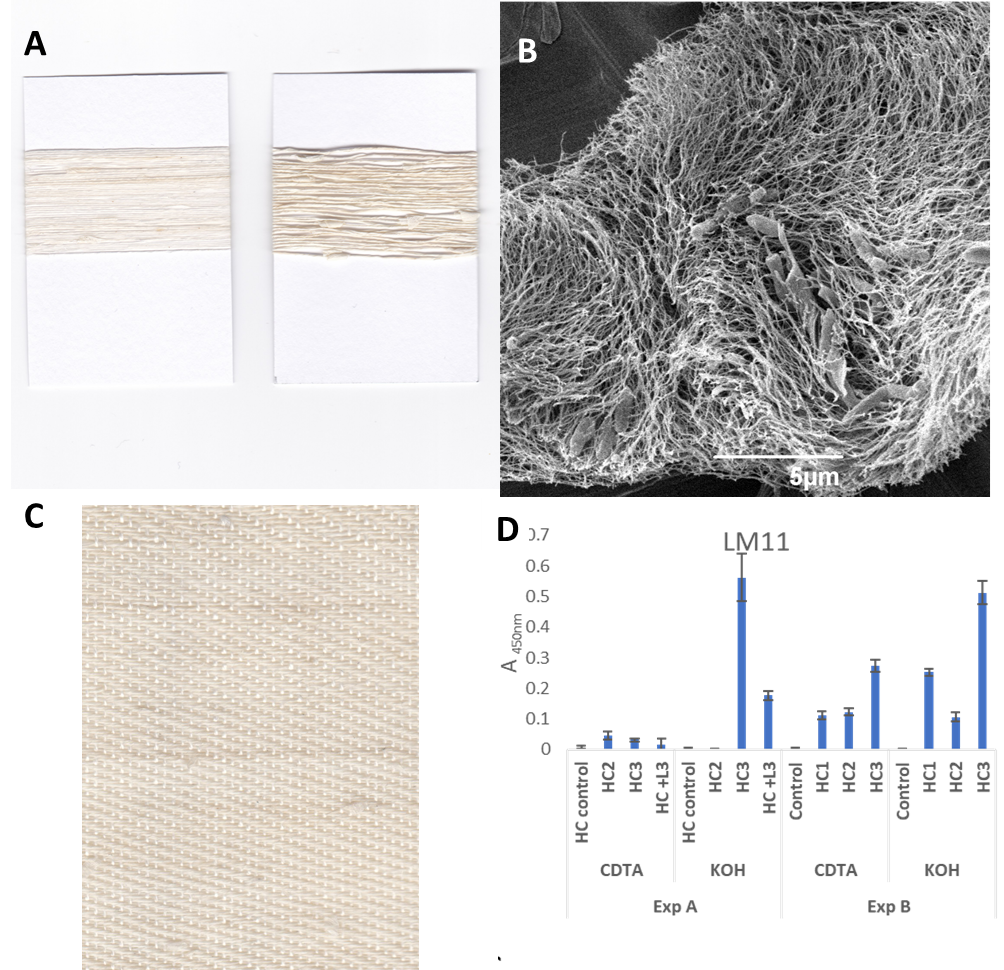
Figure 1: Novel High-Performance Textile Composites A. yarn made of bacterial cellulose; B. SEM from wet bacterial cellulose showing the network of cellulose nanofibers; C. ‘denim like’ woven bacterial cellulose; D. Composites of bacterial cellulose and hemicellulose analysed for the presence of arabinoxylan with antibody LM11.
Impact:
Further funding was secured with the same collaborators from BBSRC and EPSRC, a review paper was published as a collaboration between CNAP and RCA and collaboration with Lenzing, a major industrial producer of regenerated cellulose initiated.
Academic partners: Alexandra Lanot, University of York; Ningtao Mao, University of Leeds; Yoselin Benitez-Alfonso, University of Leeds; Miriam Ribul, Royal College of Art, London
Industrial partners: Ben Reeve, Modern Synthesis Ltd